In the era of digital transformation, companies face increasingly complex challenges to remain competitive. Advanced technologies such as Competence Centers, Digital Twin, the Industrial Internet of Things (IIoT), and Virtual and Augmented Reality (VR and AR) are revolutionising the industrial sector, offering new opportunities to improve efficiency, reduce costs, and promote innovation. In this blog post, we will explore how these technologies can help companies navigate the fourth industrial revolution, with a particular focus on the crucial role of Competence Centers.
Competence Centers: Leaders in Digital Transformation
Competence Centers are specialised structures that offer support and expertise to companies to tackle the challenges of digital transformation. Established in 2018 as public-private partnerships funded by the PNRR, these centers provide consultancy on Industry 4.0 and Smart Manufacturing, supporting innovation and industrial research projects.
In Italy, there are eight active Competence Centers, each with a specific focus on one of the Industry 4.0 technologies. They offer assessment, training, and consultancy services to help companies improve their competitiveness and innovation capacity.
Competence Centers are designed to be reference points for all Italian companies and entities, offering comprehensive support in the process towards digital transformation. Each center has a unique specialisation, which can depend on the different needs and challenges of local industrial sectors. However, the services that competence centers offer to companies are largely uniform and are divided into three main areas of intervention: assessment, training, and consultancy.
Digital Twin: From Data to Decisions
Digital Twins are virtual replicas of physical assets that, thanks to the integration of IoT, Artificial Intelligence, and Big Data, allow real-time data collection and analysis. This technology enables operational efficiency improvements, cost reductions in maintenance, and supports innovation in business processes.
A Digital Twin is not a simple static copy but a dynamic and interactive digital model, constantly updated by real-time data collected through sensors and IoT devices. This allows simulating the behavior of the physical object, predicting failures, improving performance, and optimising resource management.
Implementing a Digital Twin requires a structured approach that includes data collection and analysis, modeling, integration with AI and Machine Learning, and continuous monitoring. This approach allows adopting a continuous improvement model, reducing waste, and increasing overall efficiency.
Industrial IoT: Components, Benefits, and Challenges
The Industrial Internet of Things (IIoT) revolutionises the industrial sector by enabling machines and devices to communicate intelligently with each other. This technology offers benefits such as efficiency optimisation, safety improvement, and support for predictive maintenance.
In Industry 4.0, IoT devices (robots, machinery, equipment, and products) are equipped with sensors that provide real-time data on conditions, performance, and location of machines in production cycles. These devices do not operate in isolation but are interconnected. The maximum potential is realised through intelligent networks, which function as the nervous system for IIoT, ensuring effective and continuous communication between the various elements of the system.
The Industrial Internet of Things (IIoT) represents an integrated network of tools and applications designed to connect the entire business ecosystem, from core to edge. This end-to-end connected environment allows companies to collect and analyse real-time data, transforming it into strategic information for faster and more informed decisions.
Virtual and Augmented Reality: Differences and Benefits for Companies
Virtual Reality (VR) and Augmented Reality (AR) are advanced technologies that enhance human sensory perception. VR creates entirely virtual environments, while AR overlays digital information onto the real world.
VR is often mistakenly considered an exclusive technology for the gaming market. However, today, VR immersive solutions are an integral part of Industry 4.0 and significantly contribute to its continuous evolution. VR technologies recreate exclusively digital environments that simulate reality: 3D-modeled virtual worlds where humans can move and interact with the fictitious environment around them using a haptic interface.
AR generates an interactive experience that enhances the real world with perceptual information processed and transmitted by computers. It is one of the Enabling Technologies of Industry 4.0, overlaying digital elements (images, sounds, data) onto the real environment using tablets, smartphones, glasses, gloves, and video projections.
BI-REX’s Participation in the European Project “MOTIVATE XR“
BI-REX, one of the eight national Competence Centers, actively participates in the European project “MOTIVATE XR,” where it represents one of the Pilots. This project aims to deepen the aforementioned topics through a pilot case consisting of the assembly of a gearbox assisted by a collaborative robot mounted on an AMR (Autonomous Mobile Robot) and augmented reality headsets to support the operator. Participation in these projects is crucial for acquiring know-how and being able to support companies in their innovation paths. Thanks to these experiences, BI-REX can offer innovative solutions and targeted consultancy, helping businesses implement advanced technologies and improve their competitiveness in the global market.
Conclusion
Competence Centers play a crucial role in supporting companies in digital transformation, offering expertise and resources to implement advanced technologies such as Digital Twin, IIoT, and Virtual and Augmented Reality. These technologies not only improve operational efficiency and reduce costs but also promote innovation and competitiveness. Companies that adopt these technologies with the support of Competence Centers can gain a significant competitive advantage, enhancing their ability to adapt to the challenges of the fourth industrial revolution. With the support of specialised structures and the implementation of innovative solutions, businesses can successfully navigate digital transformation and build a more sustainable and connected future.
Authors
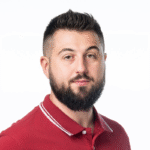
BI-REX Competence Center
Roberto Giudiceandrea is a Program Manager and Automation & Robotics Application Engineer at BI-REX. He holds an MSc in Automation Engineering from Alma Mater Studiorum – Università di Bologna
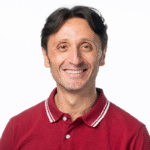
BI-REX Competence Center
Antonio Candido is a Technical Project Manager at BI-REX. He holds a PhD in Mechanical and Industrial Engineering from Università degli Studi Roma Tre.