What do workers really need from XR technologies to make their jobs easier and safer? That is the question behind Deliverable D3.3 – Industrial User Requirements and Use-Case Scenarios. Developed by CETMA and project partners, this report is a key step in making sure that MOTIVATE XR tools are designed around real people, real jobs, and real environments.
In this blog post, we share how the team gathered feedback directly from users in the field and turned it into concrete design needs. The full deliverable will soon be publicly available giving everyone a chance to see how we are building technology that truly fits the user.
Listening to the Users
The process started with conversations. Through interviews and questionnaires, partners collected honest input from people working in the five pilot sectors. What helps them? What slows them down? What do they wish XR could do?
All this feedback was then translated into what we call “User Needs”clear statements that reflect both practical and emotional needs. These were prioritised with the help of each pilot team, using a simple method that compares items in pairs. The result: a list of top needs for each pilot scenario, ranked by importance.
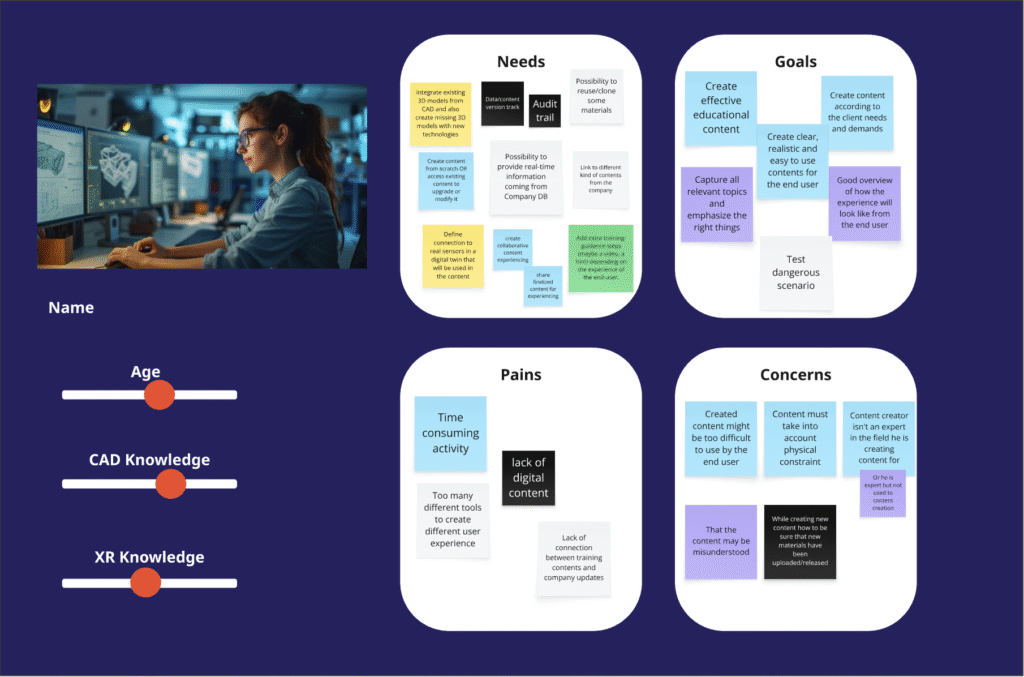
Authoring Training Material
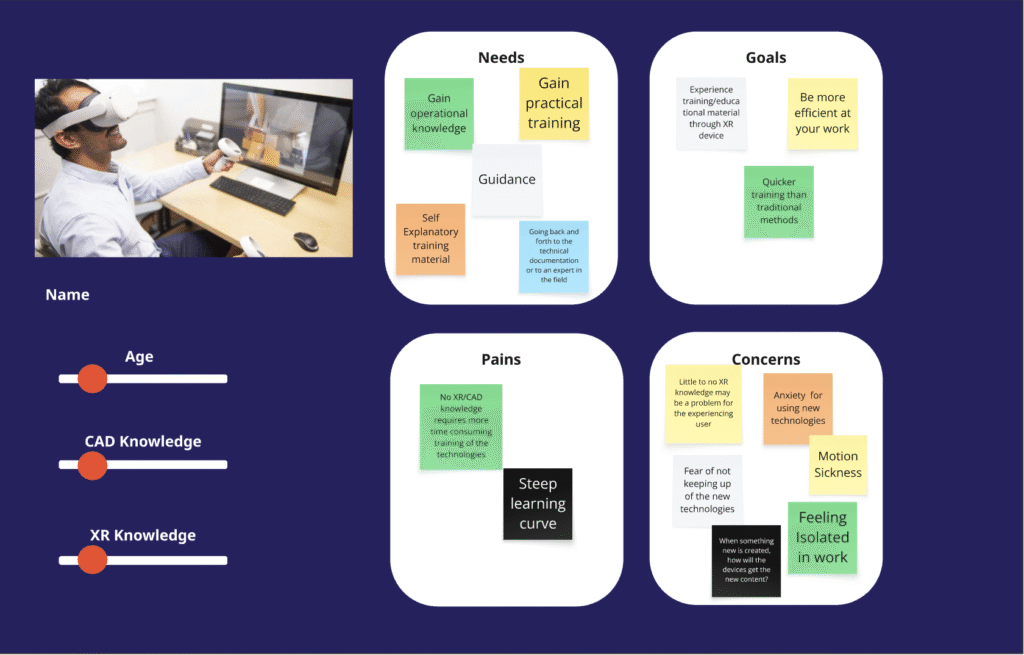
Experiencing Training Material
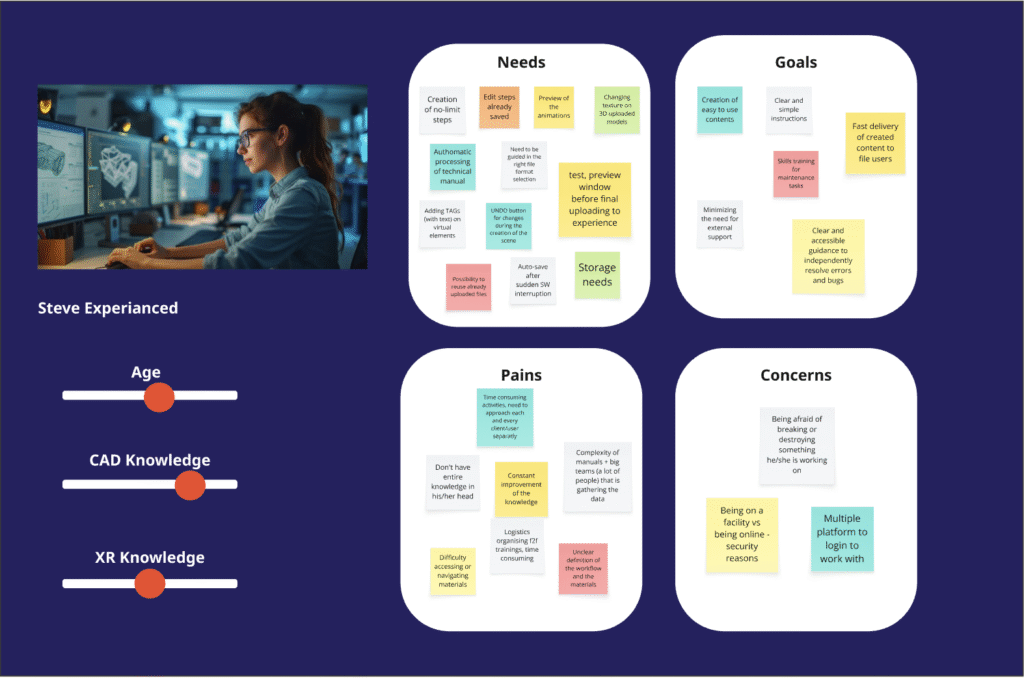
Authoring Maintenance Material
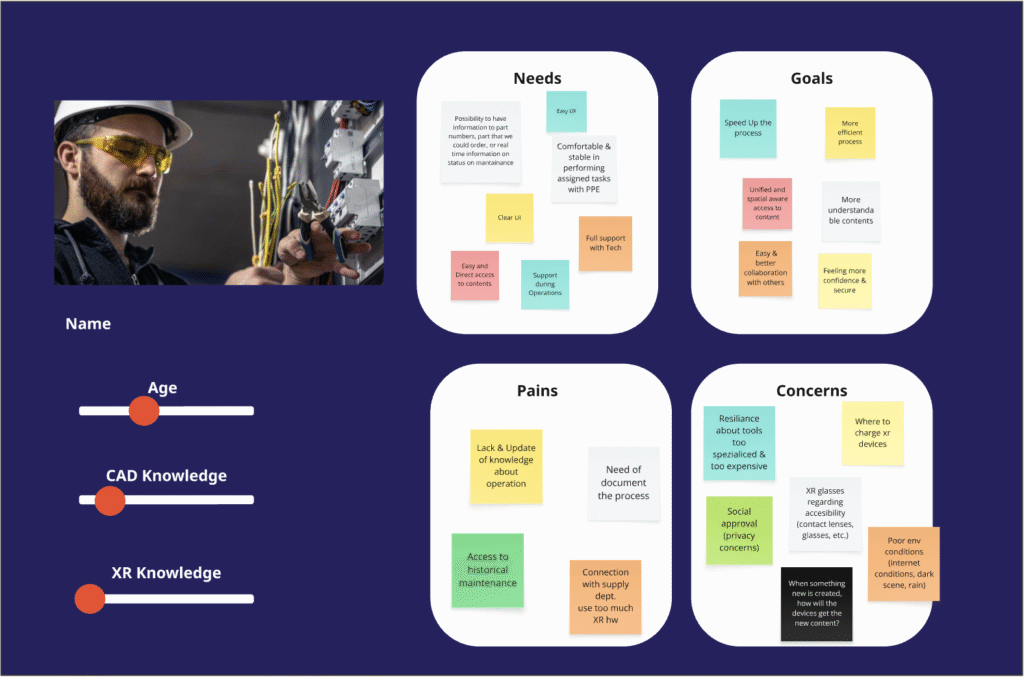
Experiencing Maintenance Material
Five Pilots, Many Contexts
MOTIVATE XR is being tested in five very different industrial areas:
- Aerospace maintenance
- Repair of household appliances
- Aluminium structure assembly
- Outdoor inspections in electricity distribution
- Working alongside robots in manufacturing
Each of these scenarios comes with specific constraints like needing to wear gloves, working outdoors under sunlight, or having no internet connection. But despite the differences, some common needs emerged: simple controls, the ability to work offline, and clear visuals.
Turning Needs into Features
After identifying what users need, the next step was to define how the XR tools should respond. These ideas became our “User Requirements” and “System Requirements” terms we use to describe the features and functions the XR tools should include.
Some of these are universal, like the ability to upload a manual or adjust screen brightness. Others are more specialised, like voice control for hands-free operation or 3D animations for complex tasks.
Importantly, every feature we plan to develop is linked back to the original user feedback. This means our future tools will not be designed in a vacuum but will directly reflect the voices of real users.
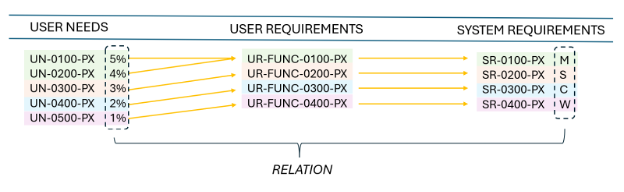
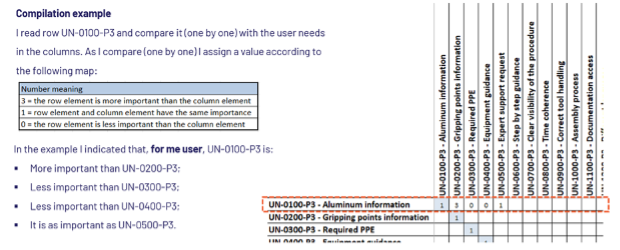
A Method for Everyone
One of the strengths of this deliverable is its method. By combining interviews, group discussions, and a clear system for prioritising needs, we have created a process that others can use too. Whether you are building XR tools for factories, hospitals, or classrooms, the same approach can help make sure your solutions match your users.
This also opens the door for future versions of the MOTIVATE XR platform to be used not only by big companies, but also by small businesses, makers, and do-it-yourself communities’ groups that usually do not have access to customised digital tools. That is a big part of what makes this project exciting.
What’s Next
This deliverable is just the first step. In the coming months, we will take these results further by refining them through additional workshops, adding input from social and legal experts, and testing them in the real pilot environments. A second, updated version will be released in Month 19.
And good news: Deliverable D3.3 will soon be publicly available on the MOTIVATE XR website. So, if you are curious about how user-centred design works in practice, or you want to see the exact process and outcomes, you’ll be able to download and explore it yourself.
References:
- The methodology adopted builds on established research in user-centered design (Lindgaard et al., 2006; Kujala et al., 2008) and applies prioritization techniques such as the AHP (Tavana et al., 2023), ensuring that the most relevant user needs guide development.
Author
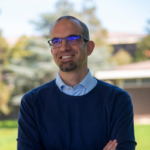
CETMA – European Research Center for Technologies Design and Materials
Luca Rizzi, Biomedical Engineer and New Product Development Unit Manager at CETMA, focuses on medical product design. He also teaches design technology and has expertise in ergonomics, risk analysis, and CE marking. His team won a Compasso d’Oro Award. He mentors SMEs through the EU’s WORTH Partnership Project and is passionate about design, ICT, 3D printing, and the maker movement.